Blast Furnace
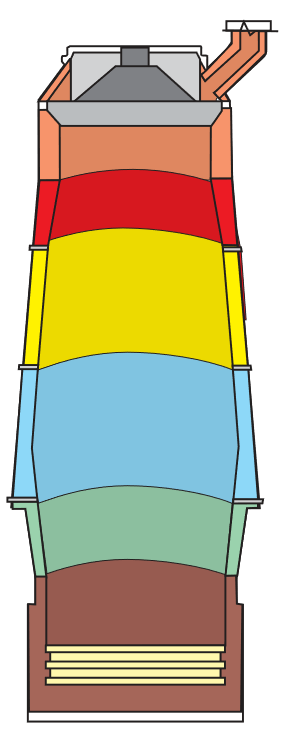
Blast furnaces reduce iron ore through a process combining coke and limestone. This is a hot blast process whereby hot preheated gases from the blast furnace stoves are injected into the bottom area. Processing through a series of tuyeres connected to a bustle pipe. The combination of temperature and carbon monoxide reacts with the iron ore reducing iron oxide into liquid iron.
The iron settles to the bottom of the blast furnace and is removed from the furnace via a taphole. The limestone provides the basis for slag that is formed to trap the impurities generated. This process and this material are removed from a tap hole as well located above the iron tap hole. Due to the extremely reducing nature of this process, refractory products must be very stable in all-respects chemically and structurally.
Refractories for Blast Furnaces
Resco's line of blast furnace refractory products have the chemical purity and mineralogy and are fired to temperature to ensure to achieve the needed properties. Typical brands are Krial 50-A, Krial 60, Krial 60-A+, and Krial 65-A for their alkali, creep, and thermal shock resistances.
Refractory Products for Blast Furnaces | |||
Brick | Castable | Mortar | |
Top | Krial 50-A | Rescocast 15GM | Metaldam |
Upper Interwall | Krial CFB | Lo-Erode GM | Metaldam |
Middle Interwall | Krial 50-A | Lo-Erode GM | Metaldam |
Lower Interwall | Krial 60-TI | Progun LC 80SCG | Metaldam |
Bosh | Rescal 90XD | Progun LC 80SCG |
Alutab |
Hearth | Krial 60 | Metaldam |